Introduction
Let’s begin this topic by acknowledging that aluminum has one of the best corrosion resistance of all metals in its pure form. But we hardly ever use metals in their pure form. They are always combined with other metals to improve specific properties for specific applications.
Pure aluminum is often combined with metals like copper (Cu), iron (Fe), magnesium (Mg) and zinc (Zn) to improve properties like strength, ductility, weldability, and anodizing. However, their introduction may reduce the corrosion resistance of aluminum alloys. In this article, we will explore aluminum corrosion’s causes, mechanism, and how we can prevent it. Let’s begin.
Article Snapshot
- Aluminum Corrosion Mechanism – Aluminum naturally forms a protective oxide layer when exposed to air, which prevents further corrosion. However, if this layer is damaged or unstable due to environmental factors, corrosion can accelerate.
- Causes of Aluminum Corrosion – Factors such as moisture, temperature variations, stress, foreign particles, and chemical exposure can trigger various types of corrosion in aluminum.
- Types of Aluminum Corrosion – There are 17 different types, including atmospheric, galvanic, pitting, crevice, and stress corrosion cracking, each with distinct causes and prevention methods.
- Prevention Strategies – Protective coatings (like anodizing, painting, and powder coating), proper material selection, cathodic protection, and regular cleaning help prevent corrosion.
- Material and Design Considerations – Choosing corrosion-resistant alloys, reducing stress on components, and controlling environmental exposure can significantly enhance aluminum’s durability.
What is Aluminium Corrosion?
Aluminium corrosion is the decay of aluminium into its oxides. Aluminium has a high affinity to oxygen, Its oxide form is its most stable form in nature. Like other metals, it wants to revert to this stable state.
Thus, when aluminum and its alloys come into contact with air, the aluminum oxidises and forms an oxide layer on the surface.
This oxide film is hard in nature. It has a powdery white or dull grey finish. Unlike the rust formed in ferrous metals such as steel, aluminium oxide sticks to the surface and does not flake.
As the layer sticks, it acts as a barrier between the unoxidized aluminum underneath and the environment. The oxidation process stops. Thus, ironically, the corrosion of aluminum can actually protect it from further degradation in certain cases.
However, if this layer is not stable and keeps getting removed, the corrosion will be much faster than in the case of steel due to aluminum’s high affinity to oxygen. This situation can occur if the metal is exposed to certain compounds such as acids in the service environment.
Causes of aluminum corrosion
Aluminum corrosion can occur due to a range of causes. Different causes are responsible for different types of corrosion in aluminum. Some of the most common factors that lead to aluminum corrosion are moisture concentration, temperature variations, stress in the material, impact of foreign particles, cyclic loads, and the presence of certain compounds and bacteria.
These causes can lead to rapid corrosion in aluminum and must be eliminated as far as possible to prevent corrosion.
Types of Aluminum Corrosion
Aluminum corrosion can be of various types. In this sections, we will cover 17 different types of aluminum corrosion, their causes and tips for their prevention. They have been sorted alphabetically for greater retention. Some types of corrosion that come later in the list may actually be more common than those coming before them.
The 17 types of corrosion mechanisms that we will cover in this section are as follows:
- Atmospheric Corrosion
- Concentration Cell Corrosion
- Corrosion Fatigue
- Corrosion in Concrete
- Crevice Corrosion
- Dealloying
- Erosion Corrosion
- Exfoliation Corrosion
- Filiform Corrosion
- Fretting Corrosion
- Galvanic Corrosion
- General Corrosion (Uniform corrosion)
- Hydrogen Damage
- Intergranular Corrosion
- Microbial Corrosion
- Pitting Corrosion
- Stress Corrosion Cracking
Let us further explore the workings of each type of corrosion, their causes and prevention.
Atmospheric Corrosion
Atmospheric corrosion is the greatest contributor to aluminum corrosion worldwide. This type of corrosion begins with environmental factors such as moisture, temperature variation, excessive wind, and pollutant concentration in the surrounding air.
These elements can interact with the aluminum surface and cause its oxidation. They can also remove the oxidized layer and oxidize the fresh layer that comes on top.
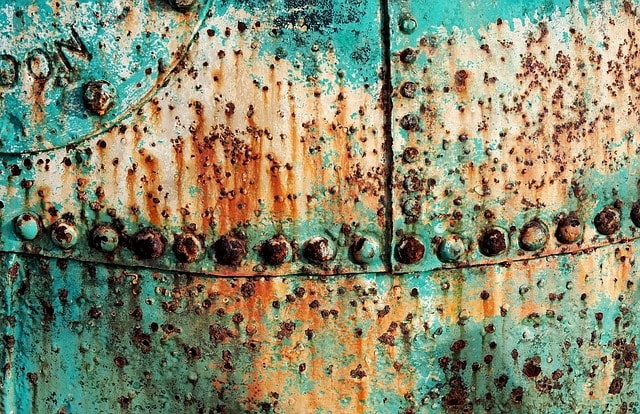
The atmospheric corrosion caused due to moisture can either be classified as dry, damp or wet corrosion depending on the moisture concentration.
We can prevent atmospheric corrosion by protecting the surface from the elements. One way to do this through anodising it. A common example of this protection method is mobile phones. Phones with aluminum bodies are anodized to protect them from elements such as water, moisture, sweat and impact.
Concentration Cell Corrosion
When two or more sections of an aluminum surface are in contact with different concentrations of a solution, an electric potential can develop. This electric potential can develop into a cell. The area with the lower concentration becomes the cathode while the one with higher concentration becomes the anode. The surface starts corroding from the anode while the cathode is protected as in any cell.
There are three main types of concentration cells that can cause aluminum corrosion:
- Metal ion concentration cell
- Oxygen concentration cell
- Active-passive cell
Metal ion concentration cell
When a faying surface (either of a pair of surfaces that are in contact with a joint) contacts water, the ion concentration increases under the faying surface and decreases in the area adjacent to crevice created by the faying surface. This difference in concentration sets up a concentration cell and corrodes the part. In this case, the corrosion starts under the faying surface. We can prevent faying surface corrosion by using protective coatings such as inorganic zinc primers.
Oxygen concentration cell
The oxygen concentration may also vary if one section of the aluminum surface is exposed to oxygen while the other isn’t. This could be due to materials like wood, plastic, dirt and rubber covering the surface. The anode is formed at the oxygen-starved region and corrosion begins. We can prevent the formation of oxygen concentration cells through effective sealing and frequent cleaning of aluminum surfaces.
Active-passive cell
The active-passive cell develops in materials that have a passive film for surface protection. It usually begins as an oxygen concentration cell due to dirt and other deposits on the surface. When the oxygen concentration cell erodes the metal under the covering material, it actually erodes the passivation layer meant to protect the part.
As a result, the active layer is exposed. The presence of this layer creates a potential difference between the active part (eroded region) and the passive film (rest of the surface). A current is setup that further erodes the active section through rapid pitting. Active-passive cell formation can also be prevented through the application of protective coatings and regular cleaning.
Corrosion Fatigue
Corrosion fatigue refers to a type of corrosion in which the combined effect of stress and corrosion on can cause the premature failure of aluminium and its alloys. Like other metals, aluminium and its alloys are assigned an endurance limit. This limit is basically a stress value below which the material will not fail due to fatigue for an infinite number of cycles.
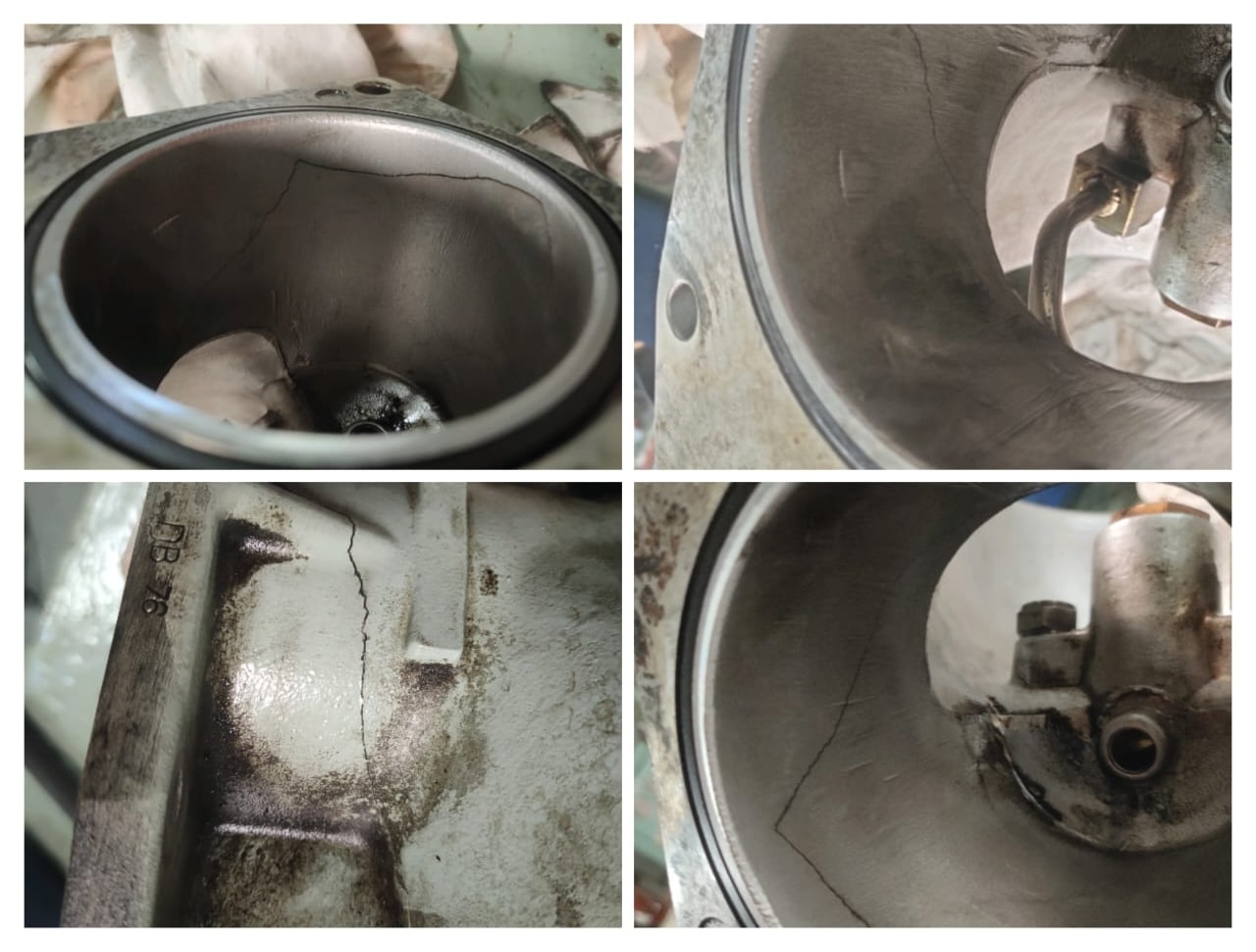
Corrosion fatigue, however, lowers this limit and the material fails at lower stress levels or after a certain number of cycles. The damage caused by corrosion fatigue is greater than what would be caused by either fatigue or corrosion by itself.
We can control corrosion fatigue and subsequent failure by reducing the number of cycles that a component is used for or by corrosion control.
When it comes to protection methods, anodizing and powder coating are not very effective. However, electrodeposition after anodizing can improve the resistance to corrosion fatigue. [1]
Corrosion in concrete
Aluminum is also used for reinforcing concrete. However, the two can have an alkaline reaction. Corrosion is aggravated by the presence of moisture, calcium chloride, and increasing alkalinity of the of the cement mixture.
The damage from the reaction may range from an etching of 0.025 mm (thousandth of an inch) per year to a complete disintegration of the structure.
This kind of undesirable reaction, however, can be avoided by covering the aluminum with materials such as plastic, oil, bitumastic, methacrylate, and asphalt among others.
It is important to note that the corrosion of aluminum in concrete is a type of galvanic corrosion or hydrogen damage. Their mechanisms are covered further in the article.
Crevice Corrosion
Crevice corrosion is a type of localised corrosion in aluminum that occurs at crevices. Crevices are any narrow gaps in the material’s surface where liquids may accumulate and form an oxygen diffusion cell. This corrosion commonly occurs near and under fastening components such as bolts and washers as these locations are more vulnerable to the collection of fluids.
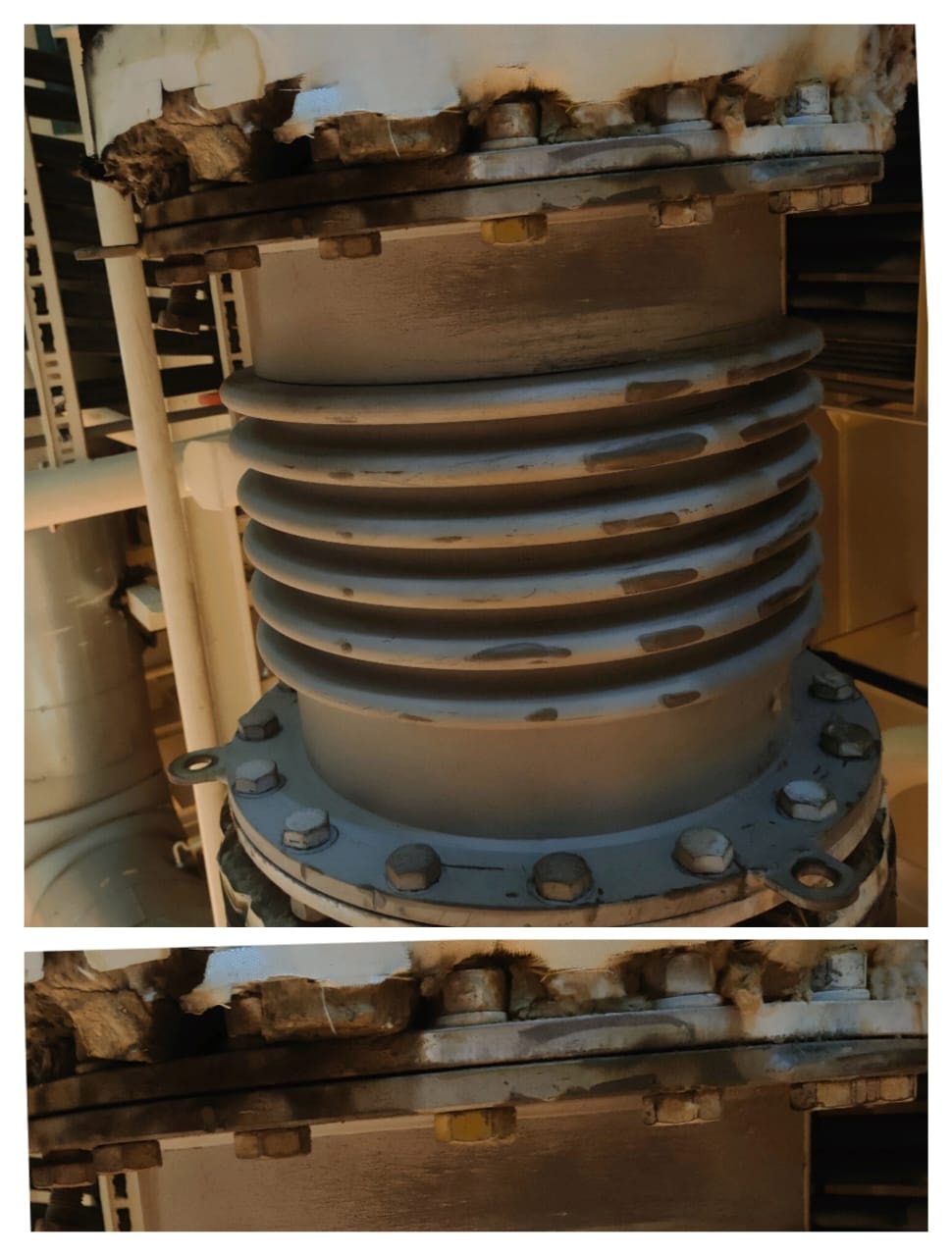
The diffusion cell is formed as the air is more readily available at the opening of the crevice compared to the area further inside the crevice. The difference in oxygen diffusion creates the cell and corrosion begins.
The damage is exacerbated by the presence of salt in the crevice liquid. Fasteners are responsible for keeping a component together. Even in cases where corrosion damage appears nominal, crevice corrosion can amplify the vibrations and cause catastrophic component failure.
Dealloying
In some aluminum alloys, such as those used in the aerospace industry, a special form of corrosion known as dealloying can take place. Dealloying, also known as selective leaching, is a type of local corrosion seem in the alloys of aluminum and other metals. It attacks specific microstructures that are more vulnerable to corrosion in the alloy.
Upon corrosion, the active elements come out of the alloy. The alloy matrix dissolves partially leaving only the more corrosion-resistant consituent in it. The resulting component looks like a sponge with holes. The material loses its strength and its no longer fit for use.
Dealloying of aluminum alloys can be prevented through four methods. We can change the environment to one with a lower oxygen content, use a suitable heat treatment, use cathodic protection, and switch to alloys with lower vulnerability to grain boundary depletion.
Erosion corrosion
Erosion corrosion is the gradual eating away of aluminum due to the impact of fluids or the particles that float with them. Such corrosion typically initiates when the protective coating on an aluminum surface is removed.
The fluid hits aluminum at a high velocity and erodes it gradually. Factors such as increasing alkalinity or acidity of the fluid make the corrosion damage worse. But even the fluid is non-corrosive, aluminum may erode if it contains solid particles such as silica and carbonate particles. These particles impinge on the surface and cause erosion.
Unlike other types of corrosion, surfaces appear exceptionally clean when suffering from erosion corrosion. An example of erosion corrosion can be seen in ship propellers churning in the water at high speeds.
Erosion corrosion can be avoided by reducing the velocity of fluid flow or altering the flow pattern where possible.
We can also prevent erosion corrosion by using harder alloys that can sustain the impact of fluid flow. Flame sprayed or welded hard facings work well. We may also reduce the concentration of silica, carbonate and any other abrasive particulates in the fluid.
Frequent surface inspections can also alert the maintenance team of the initiation of corrosion initiation. The restoration of the protective layer can prevent further corrosion.
Exfoliation corrosion
Exfoliation corrosion is commonly seen in aluminum and carbon steel. The name comes from the appearance of the corrosion effect. The corrosion seems to lift out of the surface layer as if the material is shedding scales or layers.
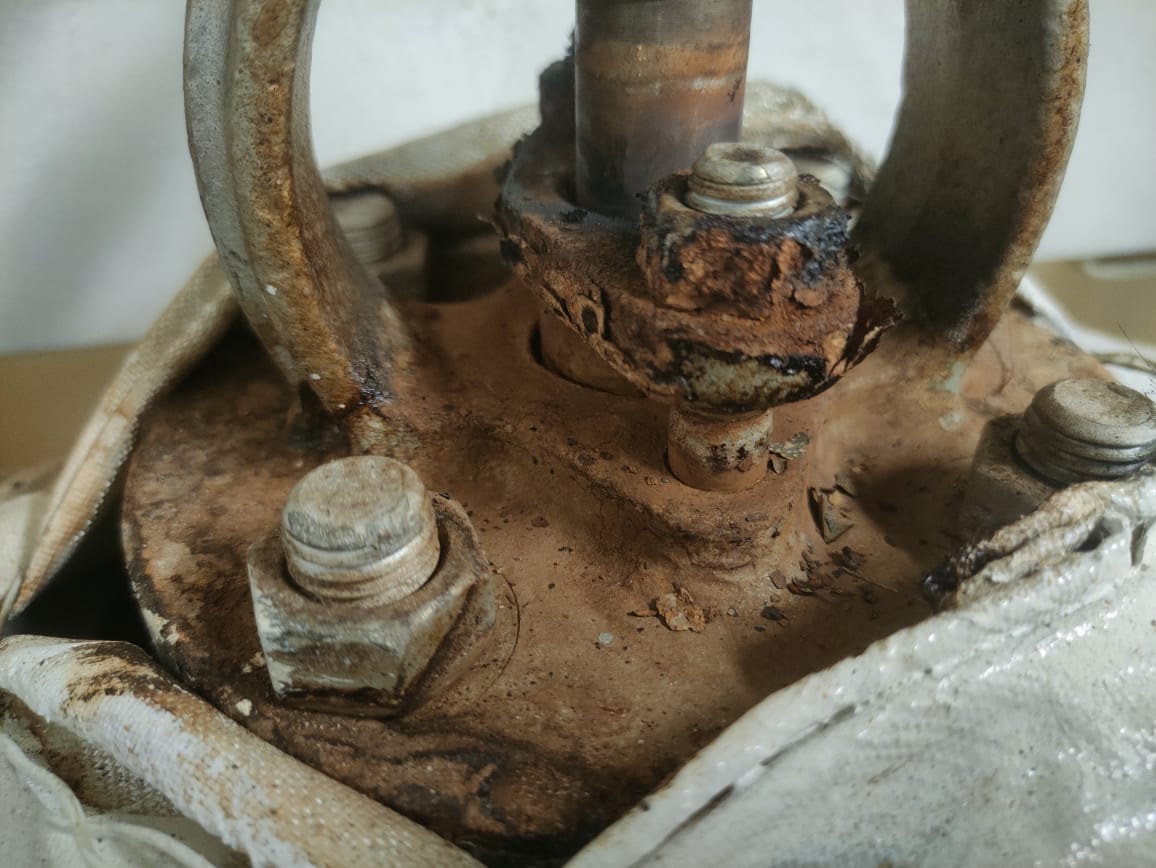
This is because the corrosion occurs under the surface and, as the corrosion compound expands, it pushes the surface out. The resulting deformation can impact the strength of the aluminum component and ultimately lead to failure.
We can prevent exfoliation corrosion by using protective coatings and subjecting the components to suitable heat treatment methods before use. Alternatively, we may also choose a more exfoliation-resistant aluminum alloy for the application.
Filiform corrosion
Filiform corrosion is seen in Al alloys that have been coated with lacquer or quick-dry paints for protection. The corrosion begins when the protection peels off or water permeates the protection and reaches the metal underneath. The initiation is at microscopic defects sites that may not be visible to the naked eye.
Once initiated, the corrosion spreads using the same mechanism as crevice corrosion. A thread-like filament forms as the corrosion propagates under the coating. As it propagates, the coating bulges until it is no longer continuous.
Filiform corrosion increases the vulnerability of a component to pitting corrosion and intergranular corrosion.
To prevent filiform corrosion, we need to eliminate the use of laquer or quick-dry paints unless necessary. When choosing protection coatings, we must opt for those with low water-vapour permeability and good adhesion characteristics.
Due attention must be given when the material is being prepared for coating. The surface must be cleaned thoroughly. They must also be inspected regularly to detect any signs of holes in the coating or filiform corrosion.
Fretting corrosion
Fretting corrosion occurs when a loaded surface rubs against another metal surface due to vibration or other variable forces. The corrosion is often seen on the surfaces near the bolts, rivets, keys, splines, bearings, etc.
For example, improperly tightened foundation bolts of a diesel generator will subject the surfaces to fretting corrosion. Over time, the amplitude of vibration increases resulting in a catastrophic failure.
Fretting corrosion may be understood as a type of erosion corrosion. The constant rubbing between metal surfaces removes the protective aluminum oxide layer and exposes the fresh layer underneath. The corrosion products, if harder than the mother surfaces, cause further abrasive action on the surfaces and remove more material mechanically. As the material comes out gradually, the vibrations become more pronounced. The corrosion propagates through the metal ultimately resulting in a fatigue failure.
Factors that affect fretting corrosion are the load force (weight of the diesel generator and combustion forces in the case of diesel generator), nature of oxidation byproducts, service environment and surface characteristics.
To control fretting corrosion, we must reduce relative motion between the surfaces. Measures such as proper tightening, vibration reduction through dampers, surface coating, improving service environment, increasing the hardness of mating surfaces through heat treatment, and use of rubber cladding can reduce relative motion and fretting corrosion.
Galvanic corrosion
Galvanic corrosion, also known as dissimilar metal corrosion, is the establishment of an electric current between aluminum and a different metal with lower reactivity compared to aluminum. The metals may be in direct contact or through a conducting medium such as an electrolyte. The current gradually consumes the aluminum.
Galvanic corrosion is one of the most popular types of aluminum corrosion. The electric current can be set up in many different service environment at sea or at land via sea water and moisture. The farther away the metal is from aluminium in the electrochemical series, the faster and more aggressive the consumption. The series is as follows:
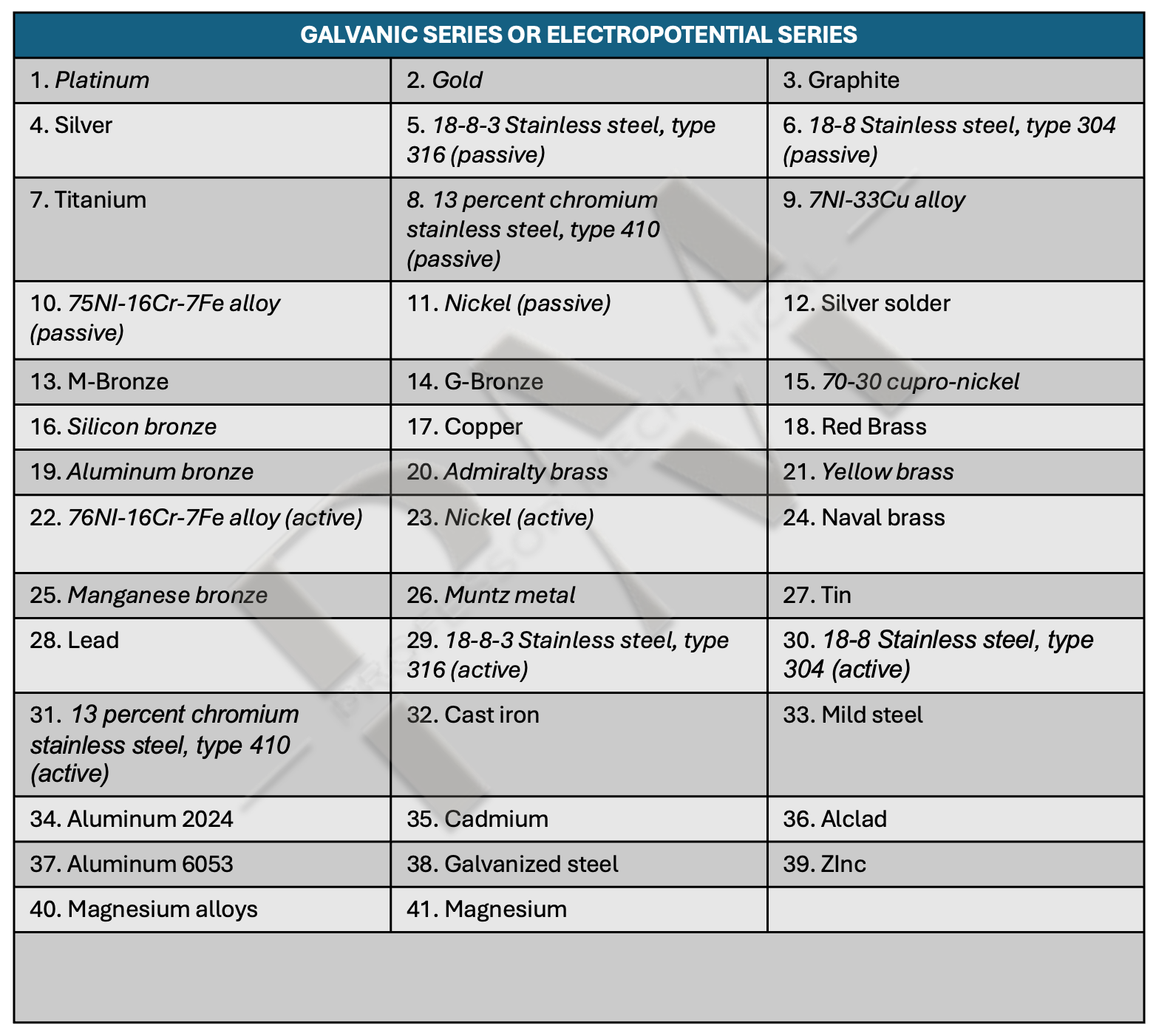
The picture above shows the galvanic or electropotential series covering 40 of the most common industrial metals in increasing order of reactivity. The metals at the beginning of the series are also known as noble metals as they are the least reactive. When any two metals from the above series are connected directly or indirectly in nature, the earlier metal acts as the cathode while the later metal acts as the anode.
In a galvanic corrosion process, the anode is eaten away while the cathode remains protected. If we want to protect aluminum from galvanic corrosion, we need to pair it with one of the metals that is lower in the electropotential series, e.g. zinc.
Once introduced into the service environment, the third metal becomes the anode and the aluminum becomes the cathode. This third metal is also known as a sacrificial anode. Zinc sacrificial anodes are often used in the industry to protect other more precious metals such as mild steel and aluminum.
General corrosion (Uniform corrosion)
This is the most common type of corrosion that exhibits a uniform layer of rust on a metal surface. The corrosion may occur due to exposure to the elements or specific causes such as an acid attack. The corrosion starts as a surface layer but may progress further if control measures are not taken. The result is an unattractive surface that can be repaired by chipping out the rust followed by a protective coating to prevent corrosion in the future.
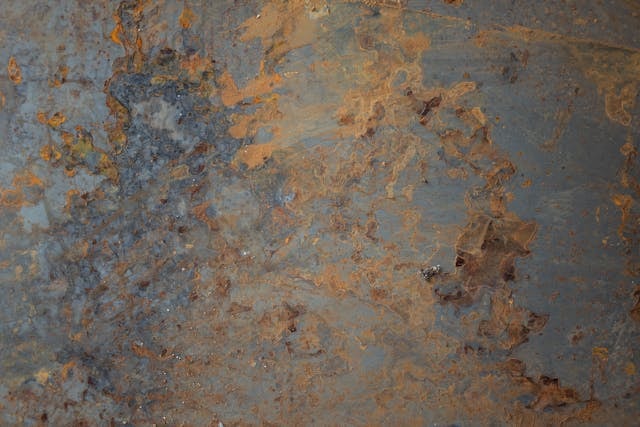
General corrosion can weaken materials structurally. However, this does not happen typically in the case of aluminium as the unsightly appearance alerts the maintenance personnel well in advance. If the action is taken while the layer is still shallow, general corrosion would not affect the part’s structural integrity.
Hydrogen damage
Hydrogen can enter aluminium or aluminium-based alloys, especially in aqueous environments. The presence of water and water vapour, or gases like nitrogen, argon or dihydrogen are ideal scenarios for hydrogen absorption.
Once in, the hydrogen gets trapped at various metallurgical sites and interacts with existing defects. These interactions adversely affect aluminium’s properties such as fracture toughness, ductility and yield strength. This phenomenon is also known as hydrogen embrittlement.
Hydrogen embrittlement can cause premature and critical failure in aluminium parts. Therefore, it is very important to prevent hydrogen ingress. We can do so by using protective coatings that act as a barrier. We may also use ionic inhibitors to reduce corrosion. Technologies such as microstructural manipulation are used for critical applications.
Intergranular corrosion
Intergranular corrosion is a type of localized corrosion seen in aluminium alloys. The microstructure of grain boundaries are chemically distinct from the center. This non-uniformity can set up a differential, and initiate corrosion at the grain boundaries.
The cracks start propagating along the grain boundaries and weaken the metal. The metal sees a decline in strength and ductility and becomes vulnerable to early failure. Heat treatment worsens intergranular corrosion in stainless steel and aluminium alloys.
We can prevent intergranular corrosion through cathode protection systems. For parts already affected with intergranular corrosion, we can use solution annealing to rectify it.
Microbial corrosion
The activities of microorganisms can also cause corrosion in various ways. This type of corrosion is called microbial corrosion.
A primary reason in most cases is the presence of water. Stagnant water, in particular, is a hotspot for microbial corrosion. In the presence of water, microbes can oxidise metals and lead to pitting corrosion of the surface.
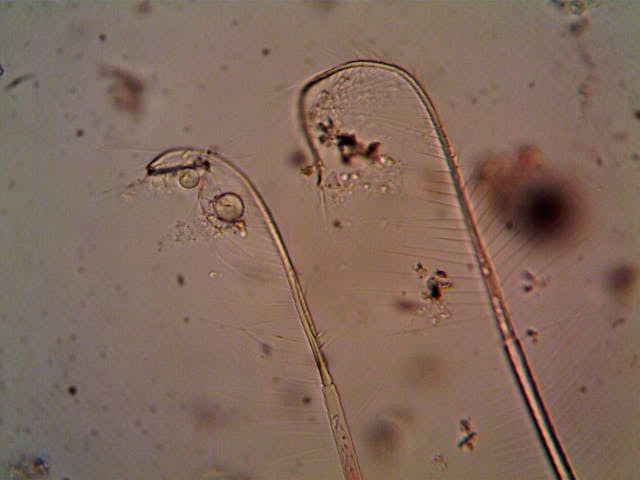
Fire-fighting pipelines, water storage tanks, and oil tanks with sufficient water content can succumb to microbial corrosion over time.
Depending on the type of microbes, aluminium corrosion may occur in the presence or absence of air. Biocides and other conventional corrosion control methods can control and prevent microbial corrosion. Draining water systems and maintaining dryness when not in use can also prevent corrosion in service.
Pitting corrosion
Pitting corrosion is an extremely common corrosion mechanism seen across the board with metal and alloys of all kinds. The event involves the formation of pits (tiny holes) in the surface of metals that are exposed to elements or corrosive solutions.
Pitting corrosion starts slow where the surface gradually begins to be covered by black or brown coloured pits on the metal surface. If left unchecked, the pits can cover the entire surface and progress into the body of the metal risking failure.
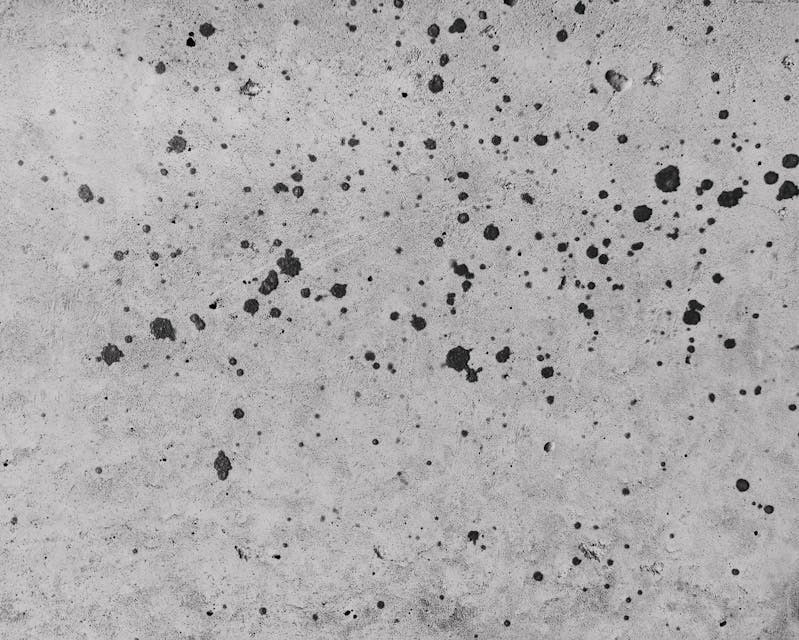
In aluminium, pitting corrosion is due to the interaction with chloride ions. Chloride ions, through saltwater or other means, disturb the protective layer of aluminium and form anodic sites where corrosion occurs rapidly.
To protect aluminium from pitting corrosion, we can use protective coatings or anodize its surface. Frequent cleaning can remove salt deposits and other contaminants from the surface. The systems must be designed using the right materials as some aluminium alloys are more vulnerable to pitting than others. High drainage efficiency further improves the system’s life.
Stress Corrosion Cracking
Stress corrosion cracking (SCC) is a special type of aluminium metal corrosion that occurs in alloys that are under tensile stress. This is the first condition. The stress may be from the manufacturing process or applied loads in the service environment, or a combination of both.
The second condition is a vulnerable alloy. Some alloys are more vulnerable than others to SCC. The third condition is a corrosive environment.
When a susceptible alloy is placed in a corrosive environment, such as saltwater, the problem worsens. The tensile stress causes the material to develop cracks which propagate through the material.
If the crack advances along the grain boundary the process is called intergranular stress corrosion cracking. The cracks may also propagate in the transverse direction which is known as transgranular stress corrosion cracking.
Protection Methods for Prevention of Corrosion
There are many ways to protect aluminium from corrosion. Let us review the most popular ones.
- The most common method is the use of protective coatings. Protective coatings create a barrier between the aluminium surface and the corrosive elements. The lack of interaction protects the metal from corrosion.
- Painting is the most affordable method to stop aluminium corrosion. The application of primer followed by a paint layer is sufficient protection. Acrylic or epoxy-based paints work best for aluminum surfaces.
- The anodizing process is also effective at aluminium protection. Anodizing is the use of an electrochemical reaction to deposit a passive, protective layer on the aluminum surface. The metal finish in iPhone bodies is an example of the anodizing process.
- To prevent galvanic corrosion, the protective layer must also have high electrical resistance.
Conclusion
Aluminium is a key metal in most industries, primarily due to its excellent strength-to-weight ratio. It also has an attractive appearance making it suitable for consumer and home appliances such as smartphones, refrigerators, washing machines and so on.
The rising demand for aluminium presents a growing challenge and a risk to the climate. There is a pressing need to conserve refined aluminium for as long as possible. By understanding the different corrosion mechanisms and prevention methods, we get a step closer to this objective.
Our understanding of aluminium corrosion mechanisms continues to improve enabling us to devise better protection strategies to stop aluminium corrosion.
References: